Toyota, a half century ago, pioneered the just-in-time strategy for supply chains—and was celebrated for its ingenuity and efficiency. With just-in-time processes in place, companies match supply with demand, producing and receiving goods only as needed, which reduces inventory costs and waste.
However, the past two years have made clear the risks involved in such streamlined operations, and companies using just-in-time may be vulnerable to even small disruptions. And while Toyota and others have maneuvered through large disruptions—such as the 2011 earthquake and tsunami in Japan, which caused the carmaker’s production to plummet by over 60% in a matter of weeks—they’ve been humbled, as almost all producers have been, by the prolonged global disruption wrought by COVID-19.
Consumers now experience delivery delays for a broad variety of products, from cars to couches to consumer electronics. Stores are subject to shortages and rising prices. Cargo ships are stuck at ports, waiting to unload.
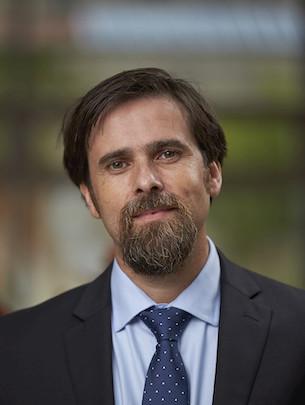
The COVID-19 supply-chain crisis, according to Prof. René Caldentey of the University of Chicago’s Booth School of Business, has raised red flags about how a relentless focus on efficiency has compromised reliability, and it has highlighted how prone the chain is to disruption. Now many companies are moving to address that. Even Toyota has been pivoting away from just-in-time and, in September, reportedly instructed some of its suppliers to store five months’ worth of semiconductors, rather than the usual three.
But just-in-time is only one piece of what has created today’s supply-chain puzzle. Companies also have to plan around the explosion in e-commerce, and an increasing need for sustainability, among other factors.
“This is a very dynamic system that keeps evolving,” said Caldentey, who warns that when the current crisis is resolved, other shocks will emerge, including some related to climate change. “This is going to keep happening. COVID has this compounding effect, but many of these problems [we’re experiencing] are not due to COVID.”
As experts look ahead to a post-pandemic supply chain, they’re considering the big questions beyond crisis management, some of which get to the core of what supply chains are even about. What do we want from supply chains, and what do we want most? Should companies focus on delivering same day or on being more environmentally friendly? Should a chain be more resilient and able to withstand disasters, or should it be efficient above all else? Should it be shorter? Closer to home? More flexible? Can it be all of those things at once?
“COVID has this compounding effect, but many of these problems [we’re experiencing] are not due to COVID.”
Make it transparent
Many supply chains are global and complex beyond our current understanding. Especially since China joined the World Trade Organization in 2001, companies have done deals with suppliers and producers all over, and they’ve come to rely on “long supply chains that snake around the globe,” according to the description of a recent National Bureau of Economic Research project. The effort, led by Harvard’s Laura Alfaro and Booth’s Chad Syverson, seeks to measure the consequences of longer supply chains and consider strategies to reduce risk. Long and lean supply chains can be, and have been, interrupted by natural disasters, cyberattacks, and political upheaval.
“A lot rides on the existence and type of substitutes available within supply chains,” said Syverson, a leading expert on market the George C. Tiao Distinguished Service Professor of Economics at Booth. “How many companies supply a given input? How many countries and geographic locations can the input be sourced from? How costly is it for inventories to be used to insure against disruptions? Can air transport be used to substitute for ships?

“Basically, if interruptions occur, how costly is it to work around them? And does it make sense for companies to spend resources to expand such options before any problems arise?”
But before companies can make significant changes to their supply-chain processes, they have to get a handle on whom they actually do business with.
“In the supply chain, we have six megaprocesses: plan, buy, make, move, distribute and sell,” said Texas A&M’s Eleftherios Iakovou. Companies work with others to accomplish the six processes, but few know all the parties with which they are directly or indirectly doing business, and few have enough information to know where the next crisis could come from, much less how to address it.
This has been a problem since long before the pandemic. The lack of transparency has enabled labor exploitation, environmental destruction, and reputational damage. Greenpeace and other activist groups have called out multinationals for using suppliers linked to problems that have ranged from dumping toxins in rivers to committing labor violations. Without full transparency, including regular audits, companies can claim they weren’t aware of the less ethical aspects of their supply chain.
“Basically, if interruptions occur, how costly is it to work around them?”
According to Booth’s Nicole DeHoratius, the first step toward transparency is for companies to map their networks fully from tier-one suppliers down, so they understand the exact composition of their supply chain.
Not all companies have a strong incentive to be more transparent. Each individual link in a chain has different goals and makes decisions in its own best interests. This is a major obstacle to sharing data within the supply chain. Consider an automaker and a brakes supplier three tiers down on the chain. The brakes supplier could be concerned that if it were to share capacity or cost information, the automaker might try to squeeze costs, or even try to bypass it and work with the supplier’s own suppliers.
“There’s just a total lack of trust on how this information would be used,” said DeHoratius, a leading expert on supply-chain management and a Booth adjunct professor.
Survey responses in the Business Continuity Institute’s 2019 Supply Chain Resilience Report indicate that 57% of global companies surveyed likely lacked complete visibility into their supply chain before the pandemic, and another 20% were unsure if they had it.

However, in light of the pandemic, “the urgency is there,” DeHoratius said. “The incentive conflicts haven’t gone away, but there is more talk about the necessity of developing this map and understanding the supply chain.”
This talk involves the need for control towers, data centers that provide real-time metrics across the supply chain. These data can be used to identify potential disruptions, suggest alternative sources, and track product flow, among other things. But DeHoratius said the effectiveness of control towers depends on the integrity of the data they utilize, and her prior work indicates that data accuracy continues to be a problem. Overall, she notes an “accumulation of errors” across the chain that include inaccurate purchase orders, port arrival data, and item descriptions for customs clearance.
Iakovou concurs that a lack of good information sharing has hindered the ability to detect problems ahead of time and respond to crises faster. Indeed, visibility, transparency, and mapping are a few of the tenets for developing resilient supply chains. His research—conducted with International Hellenic University’s Dimitrios Bechtsis, University of Cambridge’s Naoum Tsolakis and Aristotle University of Thessaloniki’s Dimitrios Vlachos—outlines a three-layer framework for supply-chain managers to improve data, integrity, and flows (of products, information, cash, and processes) across networks.
In their framework, at the cloud layer, several data streams relevant to a company’s supply chain are collected, managed, and shared across the chain according to various confidentiality levels. A Blockchain layer stores all these data securely, and the A.I. layer analyzes and processes data from the Blockchain layer to create algorithms that help supply-chain managers make decisions.
Blockchain can be used to improve transparency by streamlining transactions, notes Auburn’s Glenn Richey. He says the technology helps companies to make some data easily accessible and to keep them updated, which improves internal forecasting.
And once good data are available and accessible, they also can be shared selectively. Research that DeHoratius conducted with the Ohio State’s Elliot Bendoly and Nathan Craig provides an example of how that could help, arguing that companies can reduce the cost of uncertainty in crisis times by tracking two specific metrics: consistency (the ability of a supplier to fulfill orders repeatedly) and recovery (the ability of the supplier to fulfill orders after a service lapse). These two concepts, said DeHoratius, “have been critical in today’s dialogue about managing the pandemic disruptions to the supply chain.”
“The incentive conflicts haven’t gone away, but there is more talk about the necessity of developing this map and understanding the supply chain.”
Make it resilient
Opacity can hide risks in the chain. Before Japan’s devastating earthquake and tsunami in 2011, Toyota had close contacts with its tier-one suppliers and assumed that they were using a large variety of tier-two suppliers, DeHoratius said. After the disaster, Toyota took a close look at its tier-one suppliers and found that most were themselves using the same suppliers. The diversification of risk Toyota assumed was there actually did not exist, she says.
Iakovou argues that improving digital approaches to mapping extended supply networks is crucial. Then companies can make changes so they’re able to pivot more easily to other suppliers if needed. “Qualifying and engaging multiple suppliers of course has a cost, but, in times of disruption, those costs can be paid off multiple times over,” said Booth’s John R. Birge.

Having multiple suppliers can help both reduce the costs associated with finding and onboarding a new supplier in the midst of a crisis and avoid expensive production delays.
“If more companies react to current conditions by increasing redundancy in their supplier base, that should lead to more resilience in the overall supply-chain network,” said Birge, the Hobart W. Williams Distinguished Service Professor of Operations Management.
But building in redundancy costs more. And how much redundancy is enough? That requires accurately assessing the risk of a shock to the chain. What’s the likelihood of a tornado, energy-price shock, or pandemic that would make it worth the price of carrying extra inventory or having backup production capacity?
And what are the costs associated with assessing the risks, or not doing so? Before COVID-19, the World Health Organization put the risk of the spread of infectious diseases as below-average likelihood but above-average impact. Many companies failed to prepare, in part because of potential pushback from shareholders, and are reassessing how much it’s worth to be ready for a relatively unlikely event.
—This is an excerpt from a story first published by the Chicago Booth Review. Read the full story for more analysis by Booth faculty, who examine ways to make the supply chain more flexible, and how to move it closer to home.